The Importance of Sheet Metal Prototyping in Modern Manufacturing
In the world of manufacturing, precision and efficiency are key to creating high-quality products. One essential process that helps businesses achieve these goals is sheet metal prototyping. This technique allows manufacturers to develop and test designs before committing to full-scale production, ensuring cost-effectiveness and high performance.
What is Sheet Metal Prototyping?
Sheet metal prototyping is the process of creating preliminary versions of metal components to evaluate their design, functionality, and manufacturability. Using various fabrication techniques such as cutting, bending, and welding, manufacturers can produce prototypes that closely resemble the final product. This process is widely used in industries like automotive, aerospace, electronics, and medical equipment manufacturing.
Advantages of Sheet Metal Prototyping
1. Design Validation and Testing
Prototyping allows engineers to test and refine their designs, identifying potential flaws before mass production. This minimizes costly errors and ensures a high-quality final product.
2. Cost Savings
By catching design issues early in the process, manufacturers can avoid expensive reworks and material waste. Prototyping helps optimize production methods for efficiency and cost-effectiveness.
3. Customization and Flexibility
Sheet metal prototyping enables manufacturers to create custom components tailored to specific project requirements. It also allows for modifications and design iterations without significant delays.
4. Accelerated Production Process
Rapid prototyping techniques help reduce lead times, allowing businesses to bring products to market faster. This is particularly beneficial in industries with fast-changing technology and customer demands.
Common Techniques Used in Sheet Metal Prototyping
1. Laser Cutting
Laser cutting is a precise and efficient method used to shape metal sheets into desired forms. It allows for intricate designs and fine details without compromising material integrity.
2. CNC Machining
Computer Numerical Control (CNC) machining provides high accuracy and repeatability, making it an ideal technique for producing complex metal prototypes.
3. Bending and Forming
Metal sheets can be bent into specific shapes using press brakes and other forming tools. This technique ensures consistency and structural integrity in prototype development.
4. Welding and Assembly
Welding is crucial for joining multiple metal components together. In prototyping, this technique helps create fully functional models that can be tested in real-world conditions.
Applications of Sheet Metal Prototyping
-
Automotive Industry – Used for prototyping vehicle body panels, brackets, and structural components.
-
Aerospace Industry – Essential for testing aircraft components before full-scale production.
-
Electronics – Helps in designing enclosures and housings for electronic devices.
-
Medical Equipment – Used for producing prototypes of surgical instruments and medical device casings.
The Future of Sheet Metal Prototyping
With advancements in digital manufacturing, sheet metal prototyping is becoming even more efficient. Technologies like 3D printing, AI-driven design optimization, and automation are enhancing the speed and accuracy of prototype production. These innovations will continue to drive the industry forward, making it easier for manufacturers to create high-quality, cost-effective products.
Conclusion
Sheet metal prototyping is an essential process that helps manufacturers refine their designs, save costs, and accelerate production. By leveraging cutting-edge fabrication techniques, businesses can ensure that their products meet high standards of precision and functionality. As technology continues to evolve, sheet metal prototyping will remain a vital tool for innovation and efficiency in the manufacturing industry.
What's Your Reaction?





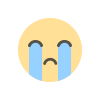
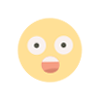